POINT
外部加熱によって熱可塑性樹脂の溶着を行う装置
インパルスウェルダーは、外部加熱(熱伝導)によって熱可塑性樹脂(プラスチック)の溶着を行う装置です。
低電圧・大電流を通電することにより、ヒータを瞬時に発熱させ、フィルムやシートの溶着に適しています。
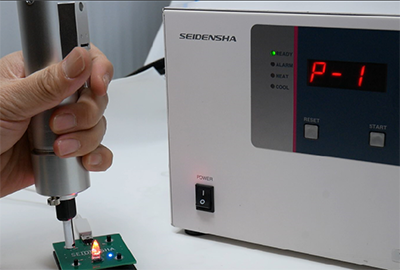
インパルスウェルダーの基本構成
インパルスウェルダーにて樹脂の溶着を行う熱源は、「ヒータチップ(先端チップ)」と呼ばれます。
加熱したヒータチップを熱可塑性樹脂(プラスチック)に直接押し当てることで溶着します。
そのため、樹脂はヒータチップと触れ合った表層から溶融していきます。
ヒータチップの形状は、線状のものだけでなく、マウント形状(カップ形状)も製作可能です。
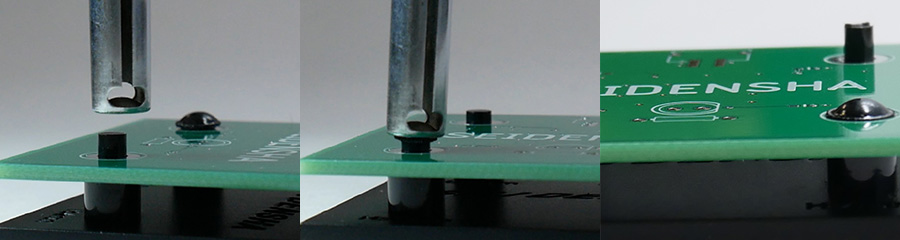
超音波溶着機のような振動を与えることがないため、粉が発生せずコンタミネーションを防止します。
振動に弱い電子基板やLEDのカシメ溶着にも適しています。また、不織布やフィルムの溶着も可能です。
インパルスウェルダーは、電源部・ヒータチップ・冷却装置で構成されます。
電源部
ヒータチップへの電力供給と加熱時間や出力の制御を担っています。トランス一体型や別体型、温度制御機能付きなどがあります。
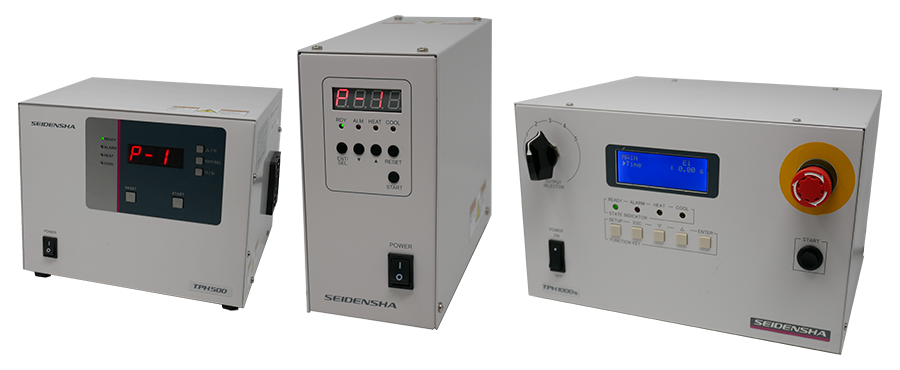
ヒータチップ
電源部(トランス)に接続され、熱源となる部分です。形状は、線状やマウント形状(カップ形状)での製作が可能です。
切削加工タイプ
削りだしで製作するため、カップ形状や長さを自由に設計することができます。プレス成型タイプに比べてボスカシメ強度が20~30%アップ(当社比)、熱解析により適正形状設計と切削加工で耐久性が向上します。
※ラインアップにない形状については、別途相談となります。
プレス成型タイプ
当社独自の設計方法により、プレス成形でありながら先端で均一な熱分布となっており、溶着の安定化が図れます。
※ラインアップにない形状については、別途相談となります。
熱電対タイプ
ヒータチップに熱電対を溶接。TPH1000Sとの組み合わせで使用すると温度コントロールが可能となります。
※ラインアップにない形状については、別途相談となります。
面シールタイプ
一般的に封止や、不織布の面シールに使用されます。
冷却装置
ヒータチップおよび溶融後の樹脂を冷却するための装置です。電源部に組み込まれているものもあります。
インパルス溶着には必須であり、通常は圧縮空気(エアー)を使用します。
マウント形状のヒータチップでは冷却用ノズルが一体化されています。
インパルスウェルダーの特長
インパルスウェルダーの特長は以下の通りです。
1.ヒータそのものを加工物に当てて使用するため、熱効率が良い
2.溶着後、加圧したまま冷却することができるので、きれいな形状を成形できる
3.ヒータ先端が瞬時に加熱されるので、機械の立ち上がりが早く、温度ムラが少ない
4.無振動での溶着が可能