POINT
周波数の選択も大事な要素
溶着物の形状や材質、溶着範囲などから使用する周波数と工法を選択します。
周波数は振動の伝達距離に関わり、溶着可能なサイズや溶着部までの距離が変わります。
超音波溶着の種類
超音波溶着は周波数特性と工具ホーン(超音波ホーン)の形状を組み合わせることにより、さまざまなプラスチック加工に対応します。
伝達溶着(溶着組立)
成形品同士を溶着して組み立てる方法。プラスチックを重ね、工具ホーンを押し当てながら超音波振動を与え、接合部分を発熱させて溶着する。
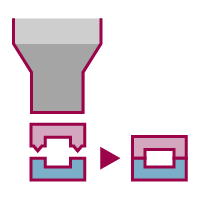
リベッティング(かしめ組立)
プラスチックと金属、あるいは異材プラスチックの成形品を固定し、組み立てる方法。熱加工に比べ、ガタが無く多点の同時加工が可能。
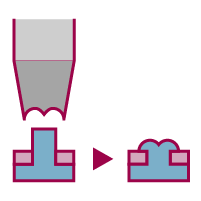
スポット溶着
重ねた2枚のプラスチック板を局所的に溶着する方法。溶着デザインは不要となるが、工具ホーン先端をプラスチックに食い込ませる必要があり、溶着する板材等の厚みは制限される。
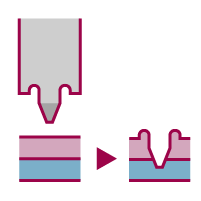
直接溶着(シール)
工具ホーンを押し当てた部分をホーン先端形状のまま溶着する方法。押し出しチューブ、ボトルなどの成形品やシートのシールなどに使用される。フィルムや不織布の連続溶着・溶断も可能。RL変換ホーンによる連続シールも可能。
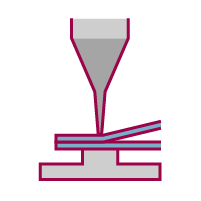
ラップバット溶着
フィルムの端部を微量重ね合わせ、一枚分の厚さに溶着する方法。エンドレスシートのつなぎ目を溶着する際に使用される。
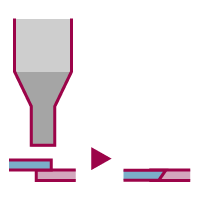
ゲートカット
工具ホーン(超音波ホーン)先端を成形品のランナー部分に押し当てて振動を加え、瞬時にゲートから切り離し部品を仕上げる方法
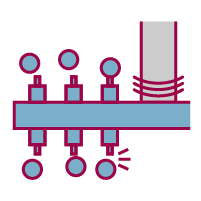
金属インサート
金属部品をプラスチック成形品の穴に圧入する方法。ほかの方式に比べ熱による変形が少なく、加工時間が短い。
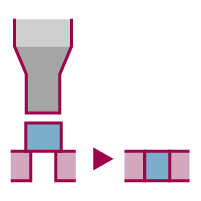
周波数の選び方
超音波溶着の各工法における周波数を選ぶにあたって基準となるのは、周波数の違いによる振動伝達距離です。超音波溶着では15~40kHzが採用されていることが多く、基本的に15~20kHzの低い周波数は溶着部までの距離がある「伝達溶着」に適しており、28~40kHzの高い周波数は表面上の「直接溶着」に適しているとされています。また、振動をプラスチックに伝えるツールの役割も果たす工具ホーンは、使用する周波数の共振体として設計されます。この設計にも周波数の伝達距離は影響を及ぼし、基本的に周波数が低い(伝達距離が長い)ほど、工具ホーンのサイズも大きくなります。では、1度に広い範囲の直接溶着はできないのでしょうか?答えは「可能」です。生産工程や設備、要求条件により取れる手段は異なりますが、例えば「共振可能な倍数で工具ホーンを大型化する」「複数の工具ホーンを隙間なく並べる」といった方法や、「低い周波数で溶着する」といった方法も考えられます。実際にクリアファイルの溶着に19kHzを使用している実例があります。一方で、ボスカシメ(リベッティング)に19kHzを選択してしまうと、ボスの中間や根本が最初に溶融してしまう「座屈(ざくつ)」と呼ばれるトラブルに繋がる可能性が高くなります。プラスチックの材質、形状、溶着条件などさまざまな要素が組み合わさるため、サンプルテストを行って要求条件に合う周波数を選ぶことをオススメします。
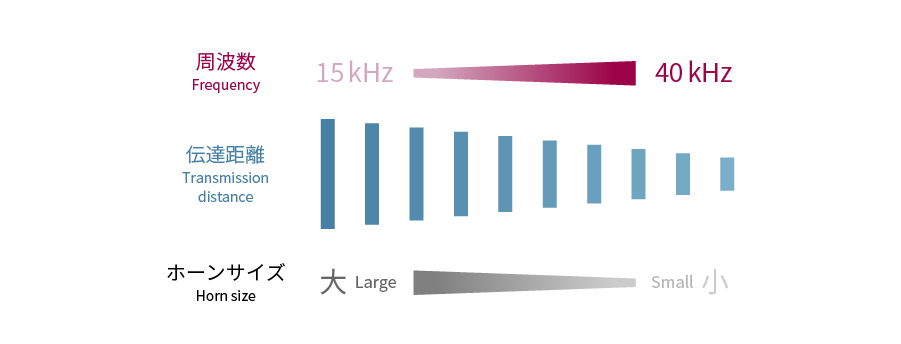