POINT
伝達溶着を可能としている秘密は溶着界面の形状にある
超音波溶着の特長である伝達溶着を効率よく行うためには、ワーク側にも溶着に適した形状を施す必要があります。
この溶着を効率化するための形状は「エネルギーダイレクター(ED)」や「溶着リブ」と呼ばれます。
溶着リブ(エネルギーダイレクター)設計の重要性
溶着リブの必要性は振動エネルギーの集中にあります。
伝達溶着の場合、溶着界面がフラット面同士であるとエネルギーが分散します。その結果、樹脂の溶けだし位置が不均一となり、下記のような症状に繋がります。
- 温度上昇の鈍化
- 溶着強度不足
- 溶着時間が長くなる
- 樹脂の劣化や破壊
- 意匠面の溶融、キズの発生
このような症状を無くすためにも、溶着リブの設計は重要となります。
超音波溶着の基本的な溶着リブ形状
ここでは、超音波溶着の基本的な溶着リブ形状について説明していきます。
超音波溶着の溶着リブ形状は大きく分けて2通りの形状があり、「ダイレクトジョイント」と「シェアジョイント」と呼ばれます。
溶着強度は基本的に溶融面積に比例するため、溶着リブの寸法や形状はワークの要件(溶着強度、外観など)に応じて設計する必要があります。溶着リブの溶融体積を大きく設計すれば溶着強度は増す傾向にありますが、必要以上の体積がある場合、バリが発生し外観や機能を損ねる可能性があります。
ダイレクトジョイント
三角形の溶着リブをワークの片方に設けます。もう片方はフラット形状です。基本的に溶着リブは同材質の溶着では工具ホーン(超音波ホーン)側、異材質の溶着では融点の高い方に設定することになります。また、発生するバリの許容範囲によりワーク形状の設計も異なります。
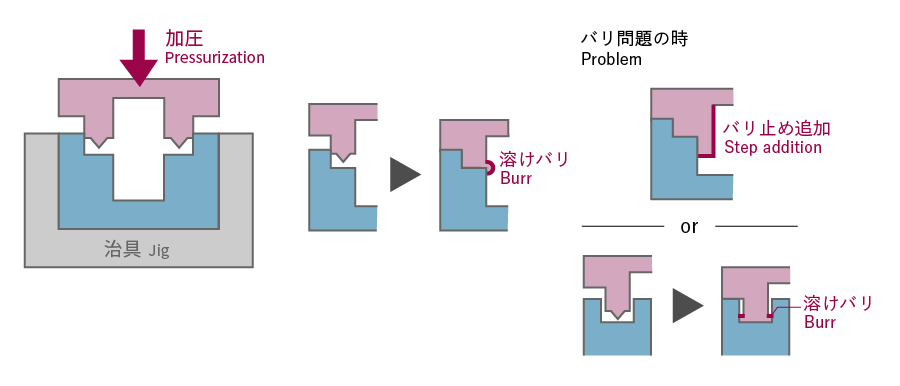
シェアジョイント
結晶性樹脂の溶着に用いられる形状です。
片方の角をもう片方の斜めの部分にぶつけるような形で設計します。
ダイレクトジョイントに比べて注意点(ワークの精度・位置関係・溶着中の膨らみ)が多く溶着の難易度としても高くなる傾向にあります。PPS・PA(ナイロン)・PBT・POM等ある程度融点が高く、溶融する領域が狭い材質に適しています。但し、これらの材質も条件次第ではダイレクトジョイントでの溶着が可能です。

シェアジョイントの場合は斜面が設けてある側のワークが力によって外に膨らむ場合が多く、治具で外形を抑える必要があります。
そのため、ワークと治具のGAP調整についても注意を要します。また、ワークの位置ズレが溶着の一部不具合となる場合が考えられるので、製品精度・位置精度が求められます。
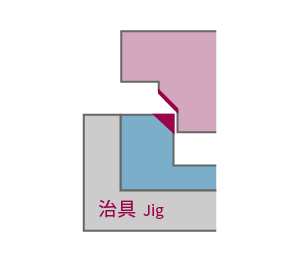