POINT
レーザの波長によって加工用途が異なる
レーザを発生させるためのレーザ媒質に何を用いるかによってレーザの種類が変わります。その種類によって波長が異なり、樹脂加工への適正が変わります。
レーザとは?
レーザ(Laser)とは、「Light Amplification by Stimulated Emission of Radiation」の頭文字を取ったものです。
日本語に訳すと「誘導放出による光の増幅」となります。
レーザとはその意味通り、光(光波)を応用した技術となります。身近なモノではレーザポインターやバーコードリーダーなどがありますが、ここでご紹介するのは、加工(産業)への応用ですので、「虫眼鏡で紙を焼く」イメージの方が近くなります。
自然光を虫眼鏡で集光させると光のエネルギーが一点に集中し、発熱して紙を焼くことができます。原理としてはレーザもこれと同じです。
ただし、自然光に比べるとレーザ光は、「単色性」「指向性」「干渉性」が高く、集光させた際によりエネルギー密度を高くすることが出来ます。この特長を利用して、樹脂を溶かしたり、接着したり(溶着)、蒸発させたり(切断)するといった様々な技術が生まれたのです。
レーザ発振の基本構造
レーザを発生させる装置は主にレーザ発振器と、それにエネルギーを供給する励起源(電源)から構成されています。レーザ発振器はおおむね下図のような構成をしており、媒質で発生した光は反射鏡によって繰り返し反射され、誘導放出によって増幅されます。これを加工に必要なエネルギーが得られるまで繰り返し、一定のエネルギーに達した光を取り出しています。レーザを発生させるレーザ媒質に何を用いるかによってレーザの種類が変わります。
媒質に炭酸ガスを用いれば気体レーザの一種である炭酸ガスレーザ(CO2レーザ)、半導体を用いれば個体レーザの一種である半導体レーザに分類されるといった形です。
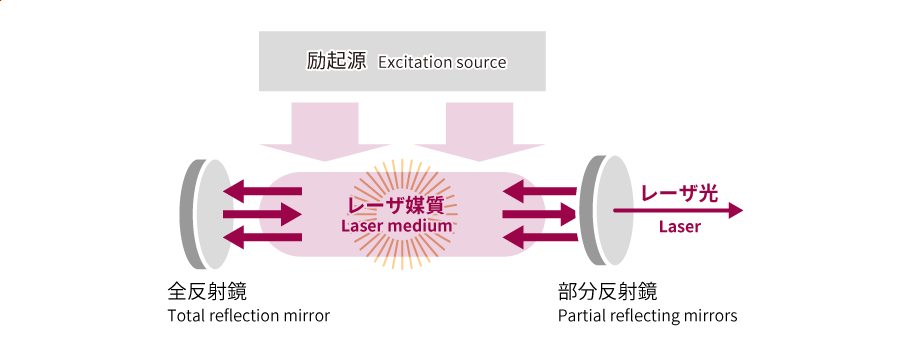
誘導放出
原子または分子に外部からエネルギーを与えると、原子または分子が高エネルギー状態になります。これを「励起(れいき)状態」と呼びます。
励起状態は不安定な状態であり、余剰エネルギーを光として放出して、原子または分子は安定状態(基底状態)に戻ります。
これが連鎖的に発生し、光を放出していくと、それぞれの光が重なり増幅されます。この現象を「誘導放出」と呼びます。
※レーザの種類によっては、誘導放出に至るフローが異なるものもあります。
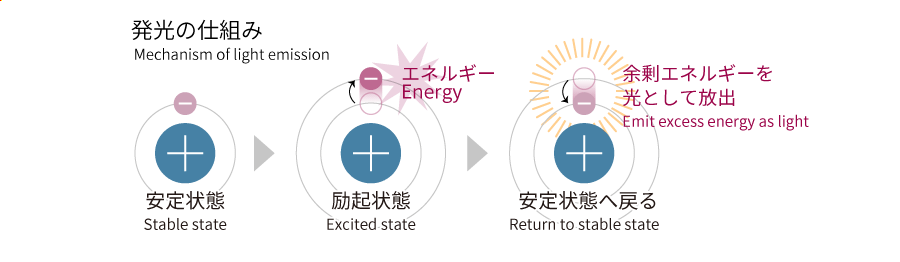
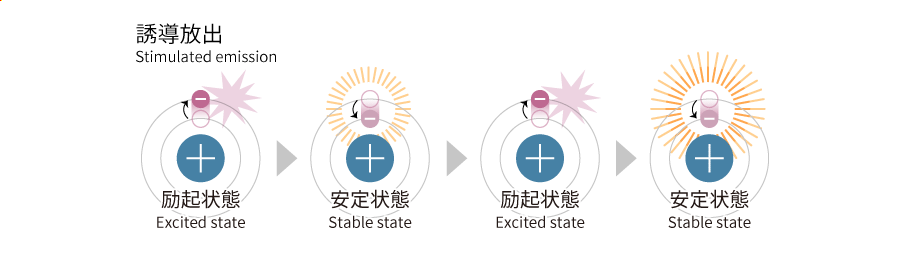
レーザ光の吸収と特性
樹脂のレーザ加工では、使用するレーザの波長によって異なる影響を受けます。
CO2レーザについて
CO2レーザは、樹脂の切断・彫刻・マーキングに最も広く使われるレーザであり、ほぼ全ての樹脂に対して高い吸収率を持っています。特にアクリルやポリカーボネートの切断・彫刻に適しており、産業用途で幅広く活用されています。ただし、熱影響を抑えるために、短パルスレーザや制御機能などによる加工条件の最適化が重要となります。
半導体レーザについて
半導体レーザは、樹脂の溶着・マーキングに適したレーザであり、特に「透過樹脂+吸収樹脂」の接合用途で強みを発揮します。高エネルギー密度のCO₂レーザや紫外レーザと比較すると、加工用途は限定的となりますが、小型で消費電力も低いため、精密機器や医療分野の製造プロセスで活用されています。